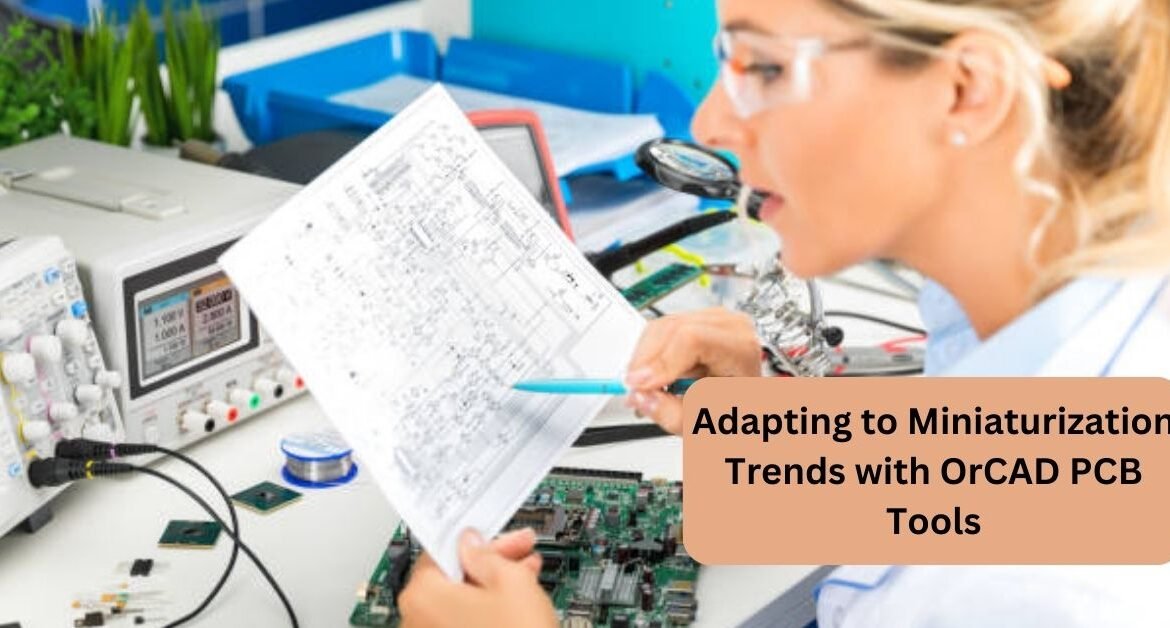
Adapting to Miniaturization Trends with OrCAD PCB Tools
Introduction
As electronic devices become smaller, more efficient, and more powerful, printed circuit board (PCB) design is evolving to meet these new demands. Miniaturization is a key trend in the electronics industry, driving innovation in PCB design to accommodate smaller components while maintaining performance and reliability.
This shift requires advanced design techniques, specialized tools, and adherence to best practices to ensure successful product development. OrCAD PCB Designer provides a comprehensive suite of tools that help engineers and designers adapt to these miniaturization trends, ensuring that circuits remain functional despite their reduced size. By leveraging advanced design methodologies, optimizing layout strategies, and integrating efficient simulation and verification processes, professionals can achieve high-density, high-performance PCBs suitable for modern applications.
The Growing Need for Miniaturization in PCB Design
The demand for compact and lightweight electronic devices is growing across various industries, including consumer electronics, medical devices, automotive technology, and industrial automation. Several factors contribute to this trend:
- Consumer Electronics: Smartphones, wearables, and portable gadgets require densely packed circuits to maintain functionality within small form factors.
- Medical Technology: Implantable and portable medical devices demand ultra-miniature PCBs for enhanced usability and patient comfort.
- Automotive Industry: Advanced driver-assistance systems (ADAS) and electric vehicle (EV) components rely on compact PCBs to optimize space and efficiency.
- Internet of Things (IoT): Small and power-efficient IoT devices depend on miniaturized PCBs to facilitate connectivity in limited spaces.
These trends underscore the necessity for designers to use sophisticated tools and methodologies to address challenges such as signal integrity, thermal management, and manufacturability.
Challenges in Miniaturized PCB Design
Component Density and Routing Complexity
As components shrink, their placement and routing become more complex. Maintaining signal integrity while avoiding interference is critical when designing high-density PCBs. Effective use of multilayer boards, blind and buried vias, and high-density interconnects (HDI) can help manage this complexity.
Thermal Management
With reduced board space, heat dissipation becomes a significant challenge. Proper thermal analysis and heat sink placement are essential to prevent component failure and maintain device longevity.
Signal Integrity and Electromagnetic Interference (EMI)
In miniaturized designs, signal integrity issues and EMI become more pronounced due to closer trace spacing and higher operating frequencies. Techniques like controlled impedance routing, proper grounding, and shielded traces help mitigate these issues.
Manufacturing Constraints
Fabrication processes for miniaturized PCBs require high precision. Ensuring design-for-manufacturing (DFM) compatibility helps reduce production errors and enhances yield rates in top-notch companies like FCPCBA.
Best Practices for Miniaturized PCB Design
1. Optimal Component Placement
Proper component arrangement is crucial for functionality and manufacturability. Keeping signal paths short and placing high-speed components strategically helps maintain efficiency.
2. Utilizing High-Density Interconnect (HDI) Technology
HDI PCBs employ microvias, blind vias, and buried vias to increase routing density. This technology helps designers create compact layouts without compromising performance.
3. Layer Stackup Optimization
Using multiple layers effectively can improve signal integrity and power distribution. Careful layer arrangement reduces crosstalk and enhances EMI control.
4. Advanced Routing Techniques
Employing differential pair routing, controlled impedance traces, and serpentine routing helps ensure signal integrity in high-speed designs.
5. Efficient Power and Ground Planes
Solid power and ground planes minimize voltage fluctuations and enhance stability in miniaturized designs. Proper decoupling capacitor placement further improves power integrity.
6. Simulation and Validation
Using simulation tools before fabrication helps identify potential issues and optimize performance. Signal integrity analysis, thermal simulations, and electromagnetic compatibility (EMC) checks are crucial steps in the design process.
The Role of OrCAD PCB Designer in Miniaturized PCB Design
OrCAD PCB Designer provides powerful features that streamline the miniaturization process and enhance overall design efficiency. Some of its key capabilities include:
1. High-Precision Layout and Routing
Advanced routing tools enable designers to handle complex layouts with ease. Features like interactive routing, auto-routing, and constraint-driven design help achieve high-density interconnects without compromising signal integrity.
2. Simulation and Analysis Tools
OrCAD includes built-in simulation and analysis tools that allow designers to validate their circuits before fabrication. These tools help ensure signal integrity, thermal performance, and power efficiency.
3. Design Rule Checks (DRC) and Constraint Management
Automated DRC features help prevent errors by enforcing design constraints such as trace width, spacing, and via placement. This ensures manufacturability and compliance with industry standards.
4. 3D Visualization and Verification
OrCAD’s 3D visualization tools allow designers to inspect their layouts in a realistic view, aiding in component placement, mechanical fit verification, and identifying potential issues early in the design process.
5. Library Management and Reuse
Comprehensive library management ensures the use of accurate component footprints and symbols, reducing design time and improving reliability. Reusable design blocks help streamline the development of similar PCBs.
Future Trends in Miniaturized PCB Design
Integration of AI in PCB Design
Artificial intelligence (AI) is playing a growing role in automating design processes. AI-powered tools assist in component placement, routing optimization, and error detection, reducing design time and improving accuracy. As AI continues to evolve, future PCB design tools are expected to incorporate more intelligent automation, predictive analysis, and generative design features that further streamline development cycles.
Flexible and Wearable Electronics
The development of flexible PCBs is opening new possibilities for wearable devices and medical applications. These ultra-thin, bendable circuits require specialized design approaches to ensure durability and performance. Innovations in materials, such as stretchable conductive inks and biocompatible substrates, are making flexible electronics more reliable for commercial and healthcare applications.
Embedded Components and System-in-Package (SiP) Technology
Embedding components within the PCB layers and using SiP technology enhances miniaturization while improving electrical performance and reducing assembly complexity. This approach is particularly beneficial for applications requiring high functionality in compact spaces, such as aerospace, medical implants, and next-generation communication devices.
Advanced Materials for Miniaturization
New substrate materials, such as liquid crystal polymer (LCP) and high-frequency laminates, are enabling better performance in miniaturized designs, particularly for high-speed and RF applications. These materials offer enhanced thermal stability, lower dielectric loss, and improved mechanical strength, which contribute to better overall PCB reliability and performance.
Conclusion
Miniaturization is a driving force in modern electronics, and adapting to this trend requires expertise, advanced tools, and strategic design practices. OrCAD PCB Designer provides a robust platform that empowers engineers to create high-density, high-performance PCBs while maintaining efficiency and reliability.
By leveraging best practices such as optimal component placement, HDI technology, advanced routing techniques, and thorough validation, designers can overcome the challenges of miniaturized PCB design. As technology continues to evolve, staying ahead of trends such as AI-driven design, flexible electronics, and embedded components will further enhance innovation in the field. For businesses and engineers seeking PCB Design services, incorporating these strategies will ensure success in developing cutting-edge electronic products that meet the demands of an increasingly compact and connected world.