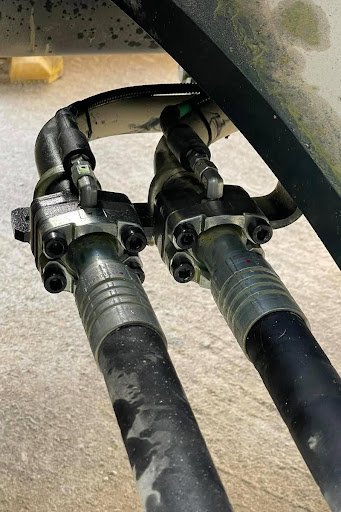
How Have Billet and On-Board Weighing Changed Over Time
Modern businesses that want to maintain their competitive advantage must prioritize accuracy together with operational speed and regulatory adherence in their operations within the current industrial environment. Two major industrial operational transformations come from the combination of On board weighing system and billet weighing systems. These advanced weighing solutions, which provide previously unheard-of accuracy and operational insights that were thought to be impossible to accomplish in real-time contexts, have completely changed how industries monitor, measure, and manage their materials.
Material handling and transportation operations have been revolutionized by on-board weighing devices that are directly incorporated into trucks and equipment. In the meantime, the businesses that produce and process metal have seen an increase in precision thanks to specialized billet weighing devices. When combined, these technologies offer advantages that go well beyond straightforward measurement, marking a substantial advancement in weight control skills.
Gaining Knowledge of On-Board Weighing Systems
The technology for measuring weight has advanced significantly with on-board weighing devices. Real-time weight information from vehicles reaches users instantly using on-board systems yet traditional weighing practices demand stopped vehicles at designated weighbridges. The innovation positions sensors together with load cells and digital displays upon numerous vehicles and equipment including trucks, loaders, forklifts, and specialized industrial machines.
These systems operate on a remarkably simple yet technically complex core idea. The weight bearing down on a car’s suspension, axles, or hydraulic systems is detected by pressure or strain sensors. Accurate weight readings are then obtained by processing the electrical impulses from these sensors, which convert the physical pressure into calibrated algorithms. Current systems provide operators with instant access to vital data through intuitive user interfaces.
The dynamic functionality of on-board weighing is what makes it so valuable. Time-consuming stops at static weighing stations are no longer necessary thanks to these systems’ ability to measure loads in motion. Through continuous measuring capabilities, this capacity improves accuracy while also transforming operational efficiency.
Uses in Various Industries
Many different industrial sectors rely on on-board weighing devices because of their flexible implementation. Through real-time monitoring operators can now prevent overloading and ensure both transportation legality within the trash management field through this revolutionary technology. Mining organizations now use this technology to maintain optimal hauling amounts across all their trucks and abide by safety restrictions.
Perhaps the industries that have profited the most from on-board weighing solutions are logistics and transportation firms. These technologies enable fleet vehicles to improve load distribution, record weight compliance during the delivery process, and verify cargo weights during loading. Businesses that deal with weight-sensitive shipments or operate under stringent regulatory regimes have found this feature to be especially beneficial.
Billet Weighing Devices: Accurate Metalworking
In the same way as on-board weighing systems revolutionize mobile operations, billet weighing system also revolutionize metal manufacturing processes. These systems are technological wonders in and of themselves since they have to provide remarkable precision under demanding industrial circumstances.
Heavy-duty platforms or cradle designs with load cells that can support large weights while retaining calibration are frequently used in the implementation. To ensure accuracy regardless of environmental circumstances, advanced systems integrate temperature compensation features that modify computations depending on thermal expansion parameters.
From initial casting to final processing, billet weighing takes place at several points in contemporary metal processing plants, forming an all-encompassing weight management ecosystem. Manufacturers can quickly identify discrepancies, modify procedures as necessary, and uphold stringent quality control throughout production thanks to this ongoing monitoring.
Innovations in Technology Advancements in Driving Systems
By removing noise from industrial vibrations or vehicle movement, digital signal processing technologies have improved the accuracy of weight readings. The wireless data transmission capabilities of today’s solutions allow for smooth integration with production control platforms, enterprise resource planning systems, and fleet management software. Weight data is converted from discrete measurements into useful business insight that informs choices thanks to this connectedness.
Similar to this, user interfaces have changed over time, moving from simple numeric displays to complex touchscreen consoles that include predictive maintenance alarms, historical data analysis, and visual representations of weight distribution. Certain sophisticated systems use augmented reality components to help operators load objects or identify possible imbalance problems before they become serious.
With the development of new composites and alloys that increase the operational longevity of parts subjected to extreme circumstances, material science has made a substantial contribution to system durability. Over time, this improved durability results in more consistent performance and fewer maintenance needs.
ROI considerations and operational benefits
Many operational benefits are provided by the use of sophisticated weighing technology, which when added together create a strong argument for return on investment. The most obvious advantage is efficiency advantages; research indicates that when cars avoid external weighing stations and take measurements while moving, productivity can increase by as much as 30%. Overall throughput capacity is impacted by the cumulative benefits of time savings that are multiplied across activities.
By removing errors that result in rejected loads, compliance fines, or problems with product quality, accuracy improvements have a direct impact on financial results. Current methods assure measurement integrity across applications by achieving accuracy rates within 1% to 2% of certified scale readings.
The complexity of the regulatory frameworks controlling industrial and transportation activities has made compliance management more and more crucial. Advanced weighing systems with automated documentation features reduce administrative expenses and minimize legal exposure by producing auditable records that show regulatory compliance.
Another important benefit is resource optimization, where accurate measurement promotes improved material use and waste reduction. This results in higher yield rates and cheaper raw material costs in manufacturing settings. It involves maximizing cargo efficiency without running the danger of overload circumstances for transportation operations.
Since avoiding overloading prolongs the life of machinery and vehicles, equipment protection is a benefit that is frequently disregarded. Businesses lower maintenance costs and increase asset service life by making sure loads stay within specified bounds, which provides long-term capital expenditure benefits.
Connectivity with Digital Environments
These days, weighing systems are essential parts of larger digital infrastructures rather than stand-alone solutions. Weight data may be easily transferred into enterprise management platforms thanks to the integration capabilities of existing systems, establishing interconnected operational environments where knowledge promotes ongoing development.
Weight measurements may be saved, examined, and retrieved from any location thanks to cloud connectivity, which makes it possible to remotely monitor and control dispersed operations. Businesses that oversee numerous locations or sizable mobile fleets find this feature very useful.
Data analytics uses trend analysis and pattern identification to turn accumulated weight information into actionable insights. Businesses can pinpoint inefficiencies, optimize production sequences or routes, and make targeted changes by looking at historical weight data in conjunction with other operational variables.
Another benefit of integration is predictive maintenance, where systems may identify unusual measurement patterns that could point to equipment problems. Proactive maintenance scheduling is made possible by this early warning feature, which lowers downtime and increases system longevity.
Conclusion:
In today’s industrial environment, onboard and billet weighing systems are technical mainstays that revolutionize material management, compliance, and operational efficiency. Their application produces quantifiable advantages in the areas of accuracy, efficiency, compliance, and resource use, generating attractive value propositions for businesses in a variety of industries.
As these technologies develop further, new insights and capabilities that improve operational excellence will be made possible by their interaction with larger digital ecosystems. Weighing systems will surely continue to be crucial parts of the industrial technology stack as industry continues its journey toward digital transformation, developing alongside other technologies that together redefine operational possibilities.