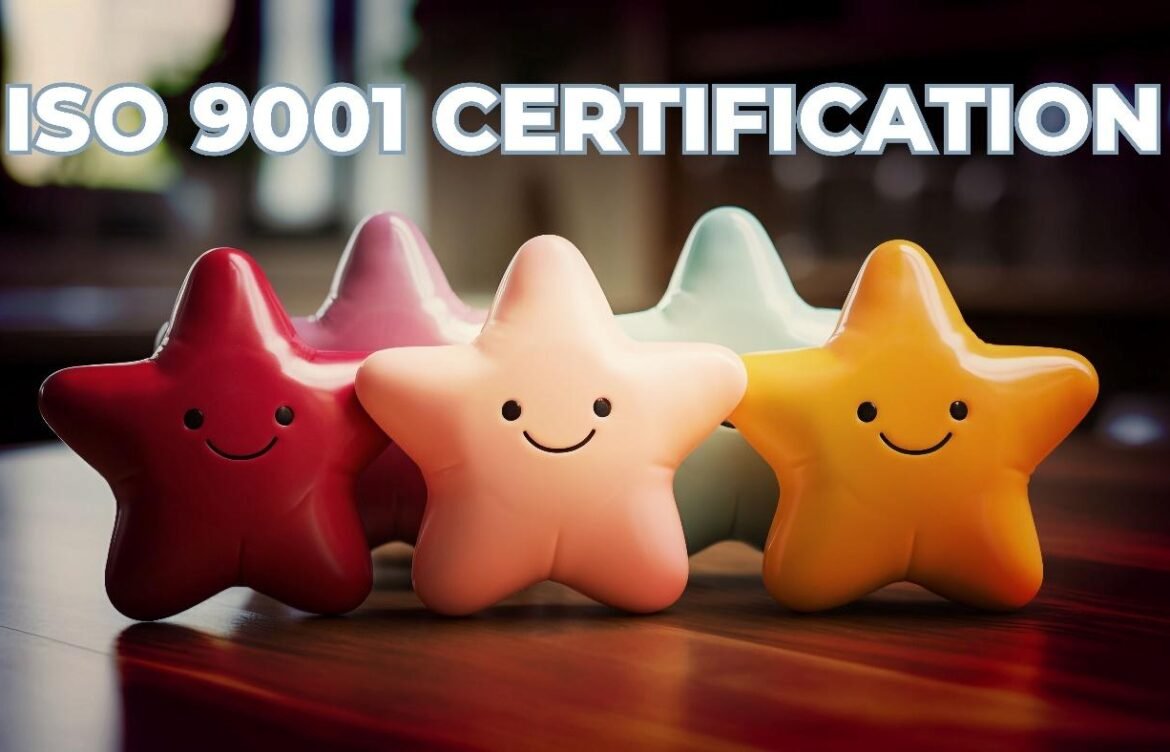
ISO 9001 Certification for Manufacturing & Industrial Companies: More Than Just a Certificate on the Wall
Introduction
Quality in Manufacturing: A Make-or-Break Factor
Let’s be honest—manufacturing is a high-stakes game. Every defective part, every inefficient process, and every unsatisfied customer costs time and money. In an industry where precision and consistency separate the winners from the laggards, there’s one name that keeps popping up: ISO 9001 certification.
But here’s the thing—it’s not just about putting a badge on your website or passing an audit. It’s about creating a culture where quality isn’t an afterthought—it’s embedded in the way you work, from the factory floor to the executive boardroom.
What is ISO 9001, Really? (And Why Does It Matter?)
ISO 9001 is the world’s most recognized quality management system (QMS) standard. It sets clear guidelines for how businesses—regardless of size or sector—can ensure their products and services meet customer expectations, regulatory requirements, and operational efficiency goals.
For manufacturing and industrial companies, this isn’t just helpful—it’s a game changer. Picture a factory where everything runs like a well-oiled machine. Minimal defects, no production delays, and a team that understands exactly what’s expected of them. That’s the power of ISO 9001 when it’s properly implemented.
But let’s cut through the jargon. Why should manufacturers care? Because in a world of supply chain disruptions, intense competition, and rising costs, you can’t afford to leave quality to chance. ISO 9001 isn’t a nice-to-have; it’s a must-have for survival and growth.
The Pillars of ISO 9001: How It Transforms Manufacturing
At its core, ISO 9001 sertifikası is built on seven principles that ensure businesses don’t just aim for quality but actually achieve it consistently. Let’s break these down:
- Customer Focus – If your customers aren’t happy, your business is on borrowed time. ISO 9001 ensures that quality is always aligned with what customers actually need.
- Leadership – Quality starts at the top. If managers don’t care about it, neither will employees. ISO 9001 ensures leaders drive a culture of excellence.
- Engagement of People – Employees who understand their role in maintaining quality are more committed, efficient, and motivated.
- Process Approach – Manufacturing is a complex web of interconnected processes. ISO 9001 helps streamline these so everything works seamlessly.
- Continuous Improvement – There’s always room to improve. ISO 9001 encourages a mindset where businesses constantly refine their operations.
- Evidence-Based Decision Making – Gut feelings don’t cut it. Decisions should be backed by hard data, reducing risks and improving performance.
Relationship Management – Your suppliers, vendors, and partners all impact your quality. ISO 9001 ensures these relationships are managed strategically.
The Step-by-Step Process to Getting Certified
The road to ISO 9001 certification isn’t a sprint—it’s a structured journey. Here’s what it looks like:
- Gap Analysis – Compare your current processes against ISO 9001 standards. Identify what’s missing or needs improvement.
- Developing the QMS – This involves documenting policies, setting quality objectives, and ensuring employees understand new procedures.
- Training & Internal Audits – Before external certification, conduct internal audits and training to ensure everyone follows the system.
- External Certification Audit – A third-party auditor evaluates compliance and issues the certification if standards are met.
- Ongoing Improvement & Recertification – ISO 9001 isn’t a “one-and-done” deal. It requires regular audits and refinements to maintain compliance.
The Real-World Benefits of ISO 9001 for Manufacturers
Now, let’s talk real impact. ISO 9001 isn’t just about compliance—it has tangible benefits that affect your bottom line.
- Reduced Waste & Increased Efficiency – Standardized processes mean fewer errors, less rework, and optimized resource use.
- Higher Customer Satisfaction – Consistency in production leads to better, more reliable products, earning customer trust.
- Regulatory Compliance Made Easier – Meeting legal requirements is a built-in feature of ISO 9001.
- Stronger Supplier & Partner Relationships – Quality extends beyond your company. A solid QMS ensures your supply chain works as efficiently as you do.
- Increased Profitability – Improved efficiency and customer satisfaction lead to stronger financial performance.
Debunking Common Myths About ISO 9001
- “It’s Only for Big Corporations” –
Wrong. Small and medium manufacturers stand to gain even more from ISO 9001. Large corporations may have dedicated quality control teams, but smaller companies often lack structured processes. ISO 9001 helps level the playing field by giving SMEs a roadmap for quality, allowing them to compete with industry giants.
- “It’s Too Expensive” –
Think about the real cost of poor quality—product recalls, returns, wasted materials, and lost customers. Compared to these expenses, the cost of ISO 9001 certification is an investment, not a burden. Many companies find that they recover their certification costs within months through increased efficiency and reduced waste.
- “It’s Just Paperwork” –
If all you’re getting from ISO 9001 is a thick binder of documents, then something went wrong in the implementation. The goal isn’t bureaucracy—it’s business improvement. When done right, ISO 9001 simplifies operations, reduces redundancy, and makes day-to-day work easier, not harder.
- “It’s a One-Time Certification” –
ISO 9001 is not a ‘set it and forget it’ process. It requires ongoing audits, employee training, and continuous improvements. Think of it as a business philosophy, not a project with a finish line. Companies that maintain compliance don’t just avoid penalties—they stay ahead of competitors by evolving with industry changes.
- “Customers Don’t Care About Certification” –
That may be true for some, but many clients, especially in B2B industries, prioritize suppliers with ISO 9001 certification. It’s often a prerequisite for landing lucrative contracts. Even when customers don’t explicitly ask for it, a proven commitment to quality gives your business an undeniable edge.
The Future of Manufacturing & The Role of ISO 9001
- Automation, AI, and digital transformation are redefining manufacturing. But one thing won’t change: the need for quality. ISO 9001 provides a framework that ensures manufacturers can integrate new technologies without compromising on consistency.
- Imagine implementing robotics, predictive maintenance, or real-time monitoring without a structured quality management system. It’s a recipe for chaos. ISO 9001 acts as a stabilizer—allowing manufacturers to innovate while maintaining rock-solid quality standards.
Conclusion
The Bottom Line
ISO 9001 isn’t just about passing an audit or checking a compliance box. It’s about building an enduring culture of quality that sets your company apart from the competition. In an industry where mistakes are costly and reputation is everything, this certification provides a structured, proven approach to long-term success.
Businesses that implement ISO 9001 don’t just improve processes—they build resilience. They gain the trust of clients, maintain high operational standards, and adapt more quickly to industry shifts. They don’t just survive market fluctuations; they thrive in them.
Manufacturing leaders who embrace ISO 9001 aren’t just keeping up with industry trends—they’re setting them. They’re the ones securing more contracts, keeping customers loyal, and adapting to market changes with agility.
In the end, this certification isn’t just a formality—it’s a competitive advantage. It signals to clients, investors, and employees that your company stands for excellence, consistency, and continuous improvement. And in an industry where every edge counts, that’s something you simply can’t afford to overlook.
If you’re serious about long-term success, it’s time to make ISO 9001 a cornerstone of your manufacturing strategy. Because the best manufacturers don’t just meet industry standards—they define them.
ISO 9001 is more than a certification; it’s a strategic tool for excellence. Whether you’re aiming for higher efficiency, stronger customer relationships, or long-term profitability, embracing this standard will help you build a future-proof manufacturing business that stands the test of time.
- No Comments
- April 3, 2025