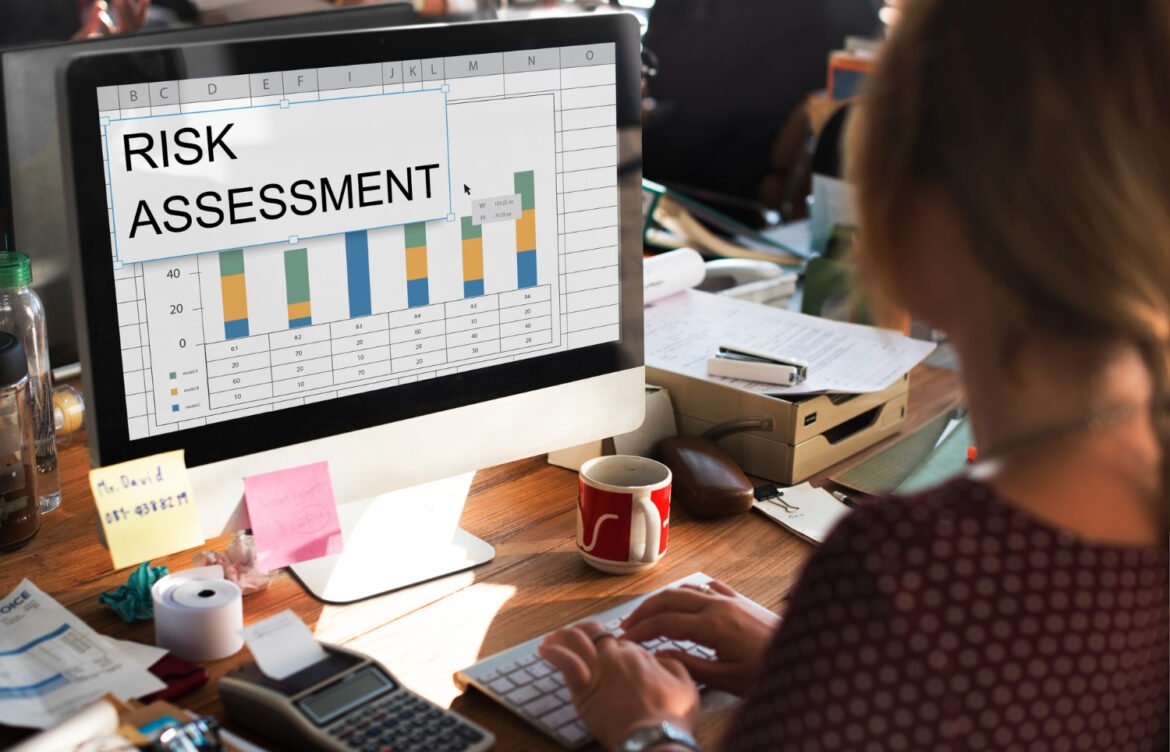
Practical Guide to TILE Risk Assessments
Managing workplace safety is essential for both employees and employers. One key tool in health and safety management is the TILE risk assessment method. Simple, effective, and practical, TILE ensures manual handling risks are identified and minimised, helping organisations protect their workforce. But what exactly is TILE, and how can you implement it effectively in your workplace?
By the end of this guide, you’ll be naturally aware of how to do a TILE risk assessment and how to implement it in various work environments. Whether you’re a manager enhancing safety protocols or an employee looking to ensure compliance, this guide has you covered.\
What is a TILE Risk Assessment?
TILE stands for Task, Individual, Load, and Environment. It’s a structured approach to assessing and managing risks associated with manual handling tasks. By breaking the assessment into these four categories, TILE enables organisations to pinpoint problem areas and take appropriate action to mitigate risks effectively.
Using TILE helps businesses comply with safety regulations, such as the Manual Handling Operations Regulations 1992 in the UK while safeguarding employees’ health and wellbeing.
Breaking Down TILE:
Task
Does the task involve repetitive movements, twisting, bending, or reaching? Analysing the nature of the task helps identify whether it places undue stress or strain on the body during manual handling.
Individual
Are individuals physically capable of performing the task safely? Employee fitness, experience, training, and potential conditions such as pregnancy or injury should be considered to determine compatibility with the work.
Load
What is being moved, carried, or lifted? Examining the weight, shape, size, and stability of the load allows you to identify potential risks more accurately.
Environment
Are there external factors that could impact safety? Environmental considerations include floor conditions, available space, lighting, temperature, and any obstacles present.
Understanding each element of TILE is the first step in effectively conducting risk assessments.
Why is TILE Important?
Manual handling injuries are among the most common in the workplace, often leading to significant downtime, reduced productivity, and financial loss. By identifying hazards early, TILE assessments not only protect employees but also reduce these associated costs.
For example, the Health and Safety Executive (HSE) found that musculoskeletal disorders related to manual handling accounted for over 480,000 injuries in the UK in 2022. This statistic highlights the importance of proactive measures, such as TILE, in reducing these risks.
How to Conduct a TILE Risk Assessment
Conducting a TILE risk assessment doesn’t have to feel overwhelming. Follow these steps to assess, document, and mitigate risks effectively.
1. Start by Observing the Task
Begin by watching the task in action. Take notes on every stage of the movement. Are employees bending awkwardly to pick up items or twisting unnecessarily? Pay close attention to repetitive actions or unnatural postures.
For instance, unloading delivery trucks may require bending, carrying heavy loads, and walking through cluttered areas. Such observations can highlight specific risk factors that need addressing.
2. Assess Each TILE Component
Now, work through TILE systematically:
- Task
Identify any significant movements that strain the body. Highlight repetitive tasks, require awkward postures, or involve handling hazardous materials.
- Individual
Evaluate whether the individual has adequate training for the task or if their physical abilities match the demands of the task.
- Load
Assess the load’s shape, weight, and stability. Is the load too heavy for a single person? Unevenly balanced loads can also pose hazards.
- Environment
Examine the workplace conditions. Are floors slippery? Is there enough room to move freely? Highlight areas with poor storage access or cluttered passages.
3. Identify Hazards and Risks
After completing your observations and TILE breakdown, create a list of obvious and potential hazards. Categorising risks as “low”, “medium”, or “high” priority ensures solutions are implemented logically and effectively.
4. Collaborate with Employees
Employees often have first-hand knowledge of the challenges they face during manual tasks. Engage team members to gain further insights and explore practical solutions to minimise risk factors.
For instance, an employee may note that frequently used items are stored too high, causing unnecessary reaching. Simple changes such as repositioning shelves or using step stools can address these concerns readily.
5. Develop and Implement Strategies
Using your assessment findings, craft a plan to minimise or eliminate risks. Options may include:
- Redesigning tasks to reduce repetitive movements
- Using manual handling aids like trolleys or hoists
- Providing adequate training to employees
- Modifying workplace layouts for better accessibility
Once in place, communicate these strategies to the team clearly to ensure adoption.
6. Regularly Review and Update Risk Assessments
Work environments evolve, and so do risks. Carry out TILE risk assessments regularly, particularly when introducing new tasks, equipment, or employees. Keeping assessments up-to-date ensures risks are controlled and compliance remains intact.
Implementing TILE in Everyday Work Scenarios
Here’s a real-world example of how TILE can be applied:
Scenario: A warehouse worker is tasked with moving boxes from a storage area to the loading dock.
- Task:
The task involves repetitive bending and lifting.
- Individual:
The worker has undergone minimal manual handling training.
- Load:
Each box weighs 25kg and lacks secure grips.
- Environment:
The storage area has uneven flooring, and the pathway to the dock is cluttered with obstacles.
Solution
After completing the TILE assessment, the employer implements several measures:
- Provides proper manual handling training.
- Offers trolleys and lifting aids to reduce strain.
- Reorganise the storage area for better accessibility.
- Repairs the flooring and removes pathway obstacles.
Such targeted actions improve safety, boost efficiency, and prevent injuries.
Common Mistakes in TILE Risk Assessments (and How to Avoid Them)
Not Consulting Employees
Ignoring input from the people performing the tasks can result in incomplete assessments. Encourage open communication during the process.
Neglecting Regular Reviews
Safety needs can change over time. Address this by scheduling periodic reassessments and ensuring they’re thorough.
Focusing Solely on Weight
While the load’s weight is critical, overlooking other factors like awkward shapes or unstable items can lead to ineffective solutions.
By avoiding these pitfalls, you ensure a reliable and actionable TILE risk assessment process.
Why TILE is a Must-Have Tool in Workplace Safety
Workplace safety goes beyond compliance; it creates a culture of care. The TILE risk assessment method provides a straightforward yet comprehensive approach to ensuring your workplace meets modern safety expectations.
Whether you’re dealing with lifting heavy boxes or reorganising office furniture, TILE equips you to address risks confidently and maintain productivity without compromising employee wellbeing.
Conclusion
Integrating TILE into your health and safety practices is simpler than you think. Make safety a priority by training your team, consulting employees, and staying proactive. Use TILE as a reliable foundation to safeguard your workforce and build trust within your organisation.
Ready to improve your workplace safety measures? Start conducting TILE risk assessments today. Read more here and Thank you.