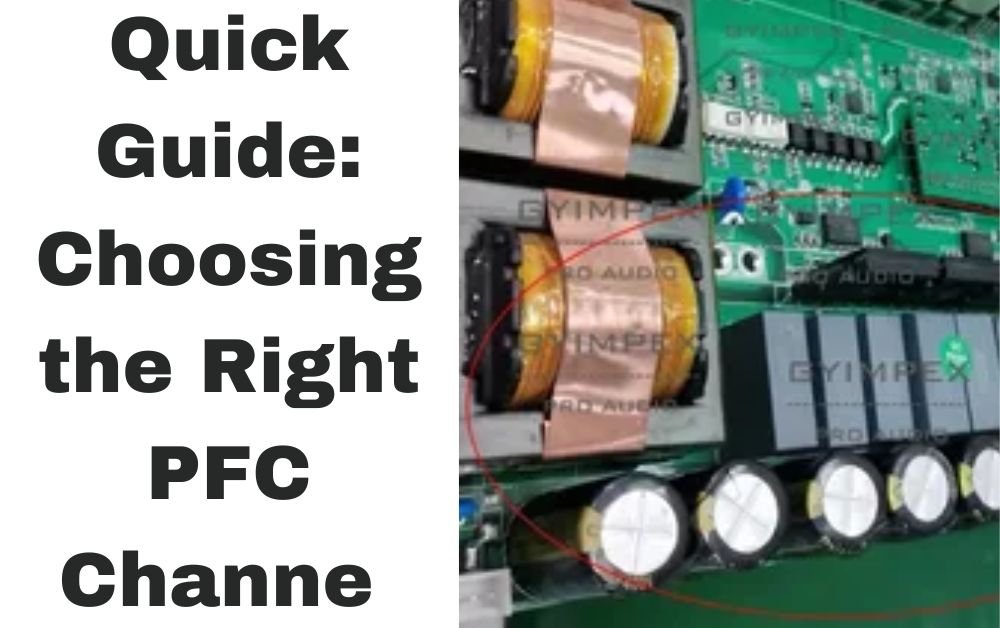
Quick Guide: Choosing the Right PFC Channel
Structural steel is a cornerstone of modern construction and manufacturing. Among the many forms of steel components used in building projects, PFC Channel—Parallel Flange Channel—stands out for its versatility, strength, and practicality. Whether you are an engineer, contractor, or fabricator, selecting the appropriate PFC Channel is crucial for ensuring structural integrity, cost-efficiency, and performance.
This guide provides a comprehensive overview of the PFC Channel, its characteristics, applications, sizing standards, and the critical considerations to help you choose the right one for your project.
This guide provides a comprehensive overview of the PFC Channel, its characteristics, applications, sizing standards, and the critical considerations to help you choose the right one for your project.
Understanding the PFC Channel
What is a PFC Channel?
A PFC Channel is a type of structural steel section characterized by a U-shaped cross-section with parallel flanges. Unlike taper flange channels, the PFC’s flanges run parallel to each other, providing consistent strength and stability throughout its length. These channels are commonly hot-rolled from mild steel and available in various sizes and thicknesses.
PFC Channels are also referred to as C-channels or U-channels, depending on regional terminology. Their structural simplicity and adaptability make them a popular choice in a wide range of applications, from industrial frameworks to residential support beams.
Applications of PFC Channel in Construction
Versatile Use Across Sectors
PFC Channels are used extensively across different industries due to their high strength-to-weight ratio and ease of installation. Common applications include:
- Structural supports for buildings and bridges
- Framing in modular constructions
- Bracing systems and load-bearing frameworks
- Industrial equipment support structures
- Stair stringers and walkways
- Vehicle and trailer frames
In each of these applications, the selection of the right PFC Channel size and grade determines the efficiency and durability of the structure.
Key Characteristics of PFC Channel
Material Composition
Most PFC Channels are made from hot-rolled mild steel, which offers excellent ductility, strength, and weldability. Some manufacturers also offer stainless steel or galvanized versions for added corrosion resistance in harsh environments.
Dimensional Standards
PFC Channels come in a range of standard sizes, typically denoted by depth (height of the web) and flange width. For instance, a 150 PFC would have a 150mm web depth, with proportional flange width and thickness.
Load Bearing and Structural Behavior
The design of the PFC Channel makes it highly effective in bearing loads along its length. However, its open shape can make it less suitable for multi-directional stress unless reinforced or used in conjunction with other structural members.
Factors to Consider When Choosing a PFC Channel
Project Type and Load Requirements
The primary factor influencing your choice of PFC Channel is the type of project and the loads it must support. For heavy-duty industrial applications, larger channels with thicker flanges and webs are necessary. In contrast, lighter structures may only require smaller-sized channels.
Perform a structural load analysis to determine the appropriate size and spacing of the PFC Channels. Consulting with a structural engineer can ensure compliance with building codes and performance expectations.
Size and Dimension Specifications
Choosing the correct size is essential. Key dimensions to evaluate include:
- Web depth (overall height)
- Flange width (horizontal sides)
- Thickness (material thickness of web and flanges)
- Weight per meter (impacts ease of handling and support)
Standards vary by country, so it’s essential to refer to regional sizing charts, such as those from BS, AS/NZS, or ASTM, depending on your location.
Material Grade
The steel grade impacts both strength and corrosion resistance. Common grades include:
- S275/S355: Common in Europe and offers a good balance of strength and ductility.
- ASTM A36: Widely used in the United States for general structural purposes.
- Grade 300/350: Used in Australia and New Zealand for medium to heavy load-bearing applications.
Surface Finish and Protection
Depending on the application environment, you may need additional surface treatment such as:
- Galvanization for corrosion resistance
- Powder coating for aesthetic and protective finishes
- Priming for painting and finishing options
For outdoor or marine environments, corrosion resistance is a top priority when selecting a PFC Channel.
Manufacturing and Supply Considerations
Availability and Lead Time
PFC Steel Beams: Some specialized or non-standard channels may require longer lead times or custom fabrication.
Working with a reputable supplier ensures access to a wide inventory and consistent product quality. Many suppliers in the UAE and GCC region maintain ready stock of common sizes for fast delivery.
Custom Fabrication Needs
If your design requires non-standard dimensions or features like pre-drilled holes or customized lengths, confirm whether your supplier provides in-house fabrication services. Custom-cut PFC Channels reduce installation time and labor on-site.
Comparing PFC Channel with Other Steel Sections
While the PFC Channel is a strong choice for many applications, it’s helpful to compare it to other steel profiles:
- I-Beam (Universal Beam): Offers superior strength for vertical loads due to its symmetrical design but is heavier and more expensive.
- Taper Flange Channel (TFC): Has sloped flanges and may offer marginal weight savings, though with a more complex fit.
- Angle Sections (L-angles): Suitable for bracing and light support but less capable for main load-bearing applications.
Choosing between these options depends on structural requirements, design preferences, and budget considerations.
Compliance and Safety Standards
Engineering and Code Compliance
Before selecting a PFC Channel, ensure it meets local and international structural standards. Compliance with standards such as EN 10025, BS 4, ASTM A36, or AS/NZS 3679 is crucial for structural safety and project approval.
Additionally, structural calculations and engineering drawings must reflect the correct sizing and load distribution for each channel used.
Certification and Documentation
Ask suppliers for mill certificates and test reports to verify mechanical properties, chemical composition, and dimensional accuracy. Proper documentation streamlines the inspection process and guarantees product reliability.
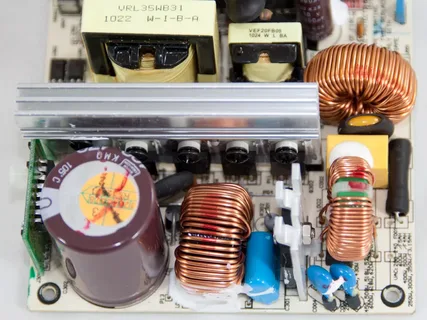
Installation Best Practices
Handling and Transport
Due to their length and weight, PFC Channels require careful handling. Use proper lifting equipment and store them in dry, stable environments to prevent warping or corrosion.
Cutting, Welding, and Fixing
PFC Channels are easily cut and welded using standard tools and techniques. However, care must be taken to preserve structural integrity during modification. Ensure that all cuts and welds are clean and sealed to avoid rust formation.
Alignment and Positioning
During installation, channels should be correctly aligned to ensure even load distribution. Use level indicators and bracing supports during fixing. Bolting or welding should be done as per structural drawings to prevent failures.
Sustainability and Recycling
Environmental Benefits of Steel Channels
Steel, including PFC Channels, is 100% recyclable, making it an environmentally friendly material. Using recycled steel in production helps lower carbon emissions and supports green building certifications like LEED.
Reuse and Disposal
Properly maintained PFC Channels can be reused in future construction projects. At the end of their lifecycle, they can be recycled into new steel products without loss of strength or durability.
Conclusion
Selecting the right PFC Channel is a critical step in ensuring the strength, efficiency, and longevity of your structural project. From understanding the different sizes and grades to considering surface finish and load-bearing requirements, every aspect plays a vital role in the success of your build.
This quick guide provides a solid foundation for evaluating your options, but always consult with engineering professionals and certified suppliers to ensure the best outcomes. A well-chosen PFC Channel not only supports your structure—it supports the success of your entire project.
For more insightful articles related to this topic, feel free to visit: futuretechradar